The new way of process control with FOCUS-1 in automation
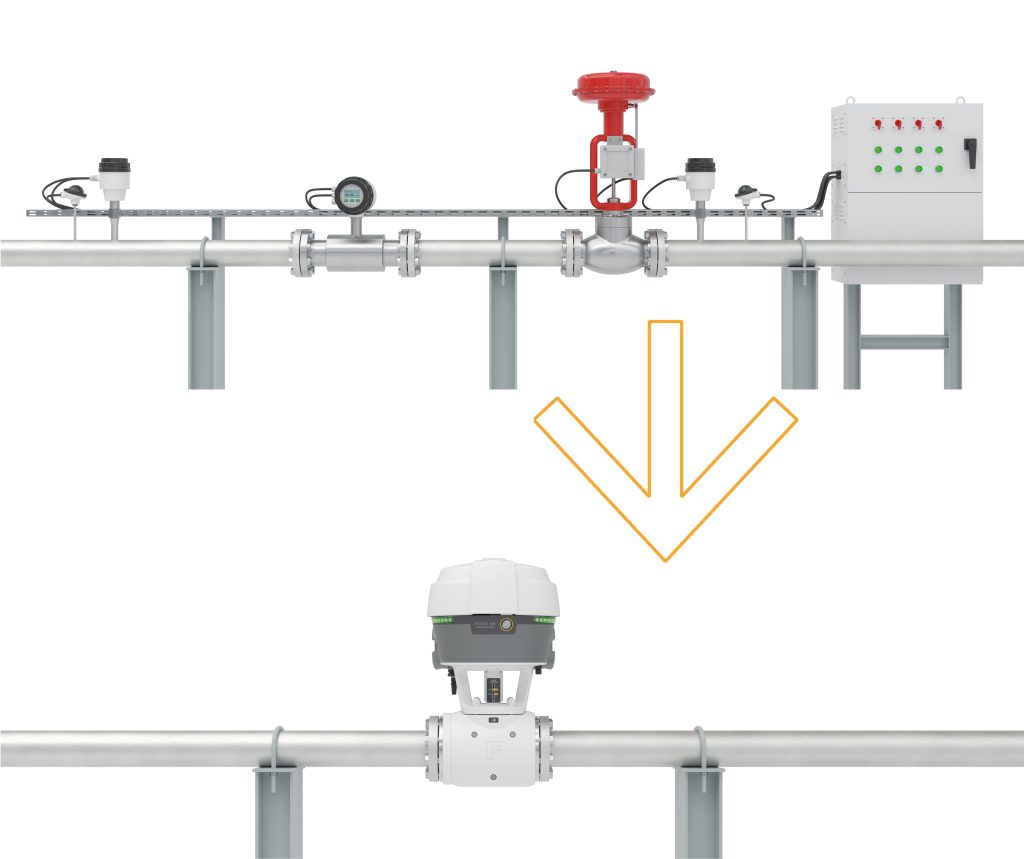
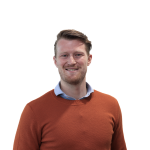
George Borst
Responsable du développement commercial
April 11, 2025
For decades, process control has relied on traditional methods that often require multiple components, extensive programming, and complex integration. However, as industries move towards smarter, more efficient automation solutions, there’s a need for a new way of process control—one that is simpler, more precise, and seamlessly integrated.
That’s where FOCUS-1 comes in, a game-changing solution that revolutionizes how industrial plants manage flow, pressure, and temperature regulation. Instead of relying on external PID controllers, multiple sensors, and complex wiring, FOCUS-1 integrates everything into a single, intelligent device.
The old way: Position-based process control
Historically, industrial control valves have operated on a position process control basis. This means:
- The control valve receives a setpoint for position (e.g., 50% open), which determines how much fluid flows through the pipeline.
- A separate PID controller in a PLC or DCS calculates adjustments based on feedback from external sensors.
- Additional flow meters and pressure sensors are required to verify the actual flow and pressure levels.
While this method has been standard practice, it comes with several inefficiencies:
- Lag and overshooting: Since the control valve isn’t measuring the actual flow, its movements can cause fluctuations, leading to process instability.
- Excessive tuning and calibration: Engineers must fine-tune PID loops and manually integrate separate sensors to ensure accuracy.
- Increased system complexity: Multiple components require additional installation, programming, and maintenance.
Also read our blog ‘Traditional process control vs. Smart Meter Valves’.
The new way: Direct process variable control
With FOCUS-1, industries can now transition to a more intelligent and efficient approach—controlling directly on the desired process variable rather than the valve’s position.
Here’s how it works:
- Instead of setting a valve position, the FOCUS-1 receives a direct setpoint for flow, pressure, or temperature.
- The built-in sensors measure real-time flow and pressure values, eliminating the need for external sensors.
- An integrated PID controller processes the data and automatically adjusts the valve position for optimal control.
- The entire system communicates seamlessly with the PLC or DCS, using standard industrial protocols like PROFINET, HART, and Modbus.
The key benefits of the new way of process control
By eliminating unnecessary components and optimizing control performance, FOCUS-1 provides significant advantages over traditional control methods.
1. More accurate and stable control
- Since FOCUS-1 directly measures flow and pressure, control responses are faster and more precise.
- Overshooting and deviations are minimized, resulting in a more stable process.
- Less manual tuning is required, reducing engineering effort.
2. Simplifies system architecture
- Eliminates the need for separate PID controllers in PLCs/DCS, reducing programming and integration work.
- No additional sensors are required, saving space and lowering procurement costs.
- Reduces system wiring and piping complexity.
3. Reduces energy consumption
- Traditional control methods often lead to unnecessary energy waste due to inefficient valve movements and excess pumping.
- By controlling directly on flow and pressure, FOCUS-1 ensures minimal energy consumption while maintaining optimal process conditions.
4. Improves maintenance and predictive insights
- FOCUS-1 continuously monitors valve performance and process conditions, detecting early signs of wear or inefficiencies.
- Predictive maintenance models reduce unexpected failures and extend equipment lifespan.
- Moins de temps d'arrêt means higher productivity and lower operational costs.
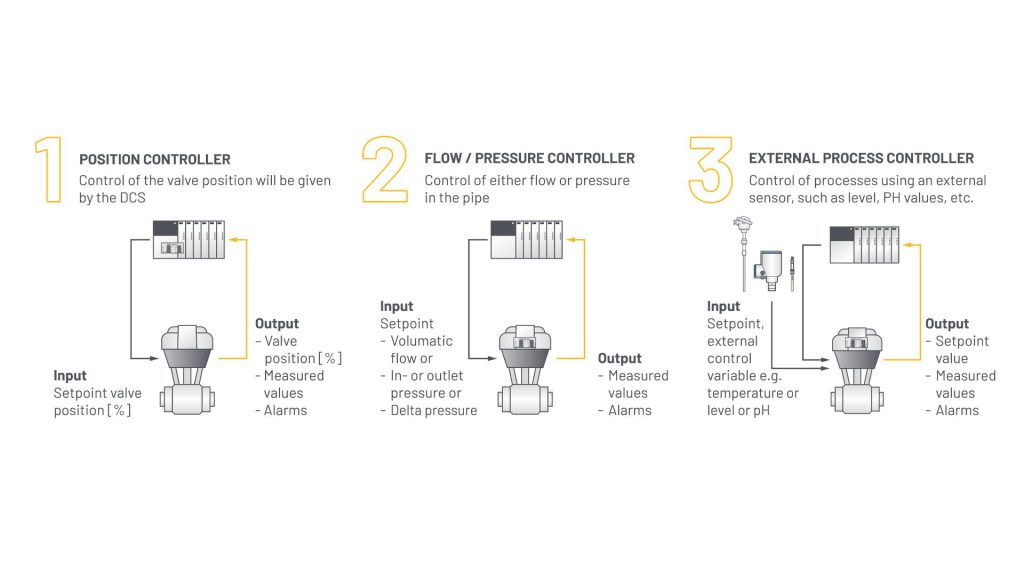
Expanding control possibilities with external process sensors
FOCUS-1 doesn’t just control based on its own internal measurements—it can also integrate external sensors for advanced process control.
For example:
- Level control: Connect an external level sensor to FOCUS-1, and it will regulate flow to maintain a constant tank level.
- pH or temperature control: The device can receive input from a pH or temperature sensor and adjust flow accordingly.
- Heat exchanger optimization: By integrating external temperature sensors, FOCUS-1 can optimize heat transfer efficiency.
This flexibility opens new possibilities for automation, allowing plants to control their processes with greater precision and adaptability.
Real-world use cases of the new way of process control
Industries that have adopted FOCUS-1 for direct process variable control have seen measurable improvements in efficiency and cost savings:
- Chemical processing plants: Achieved 40% more stability in flow control, reducing raw material waste.
- Food & beverage production: Improved consistency in ingredient mixing and batch quality control.
- Water treatment facilities: Optimized pressure and flow regulation, leading to lower energy consumption.
- Pharmaceutical manufacturing: Enhanced precision in temperature and pH regulation, ensuring compliance with stringent regulations.
Read more case studies here.
The Future of Process Automation with FOCUS-1
By introducing a new way of control, FOCUS-1 paves the way for simpler, smarter, and more efficient automation. As industries strive for greater precision, lower costs, and improved sustainability, adopting direct process variable control will be key to staying competitive.
Conclusion
Traditional position-based control methods are becoming obsolete. FOCUS-1 provides a modern, integrated approach that directly controls on flow, pressure, and temperature—simplifying automation, improving accuracy, and reducing costs.
Want to learn more about how FOCUS-1 can transform your process control strategy? Get in touch with our experts today!
Book your free consultation call today!
Want to read more about FOCUS-1?
Also make sure to read our blogs about: