In the high-stakes world of chemical manufacturing, even a few minutes of downtime can translate into operational chaos and significant financial losses. This case study explores how a leading chemical manufacturer in Antwerpen successfully eliminated downtime and optimized operations by implementing the FOCUS-1 smart metering valve, enhancing both control accuracy and energy efficiency.
Company Background
A major global chemical manufacturer, with a history spanning over a century, operates across multiple sectors, including Chemicals, Materials, and Agricultural Solutions. For confidentiality reasons, the company’s name is not disclosed. This organization is known for its commitment to sustainability and innovation, with operations in numerous countries worldwide, employing a vast workforce.
This case study highlights one of their largest and most integrated production facilities, situated in a key industrial region in Europe. The facility produces a diverse array of chemical products and intermediates. A critical aspect of the facility’s operations is its condensate infrastructure, which provides a steady supply of steam to various units through an extensive network of pumps and pipelines.
Process Description & Initial Challenges
The Antwerpen site operates multiple plants that rely heavily on a steady supply of steam, generated from condensate distributed from the site’s energy factory. The condensate distribution system uses a ring network and pumps to maintain the necessary flow and pressure, ensuring all plants have the resources required for their chemical production processes.
Previously, the site used a pressure-reducing valve to manage this flow and pressure. However, the system struggled with maintaining accurate control, leading to inefficiencies and increased operational challenges. The pressure-reducing valve failed to provide the precision needed, making it difficult to balance the pump operations and achieve optimal energy efficiency. Consequently, a more accurate and efficient solution was sought.
Challenges in Maintaining Accurate Flow and Pressure Control
The primary challenges faced included:
- Inaccurate flow and pressure control with the existing pressure-reducing valve.
- Difficulty in balancing pump operations to maintain energy efficiency.
- Risk of downtime due to valve or pump failures, potentially leading to significant operational disruptions.
Downtime Metrics and Associated Risks
In the event of a system failure, operators had to manually start a redundant pump. If this redundant pump and valve also failed, it posed a significant risk of either insufficient or excessive flow and pressure within the ring network, which could halt production processes.
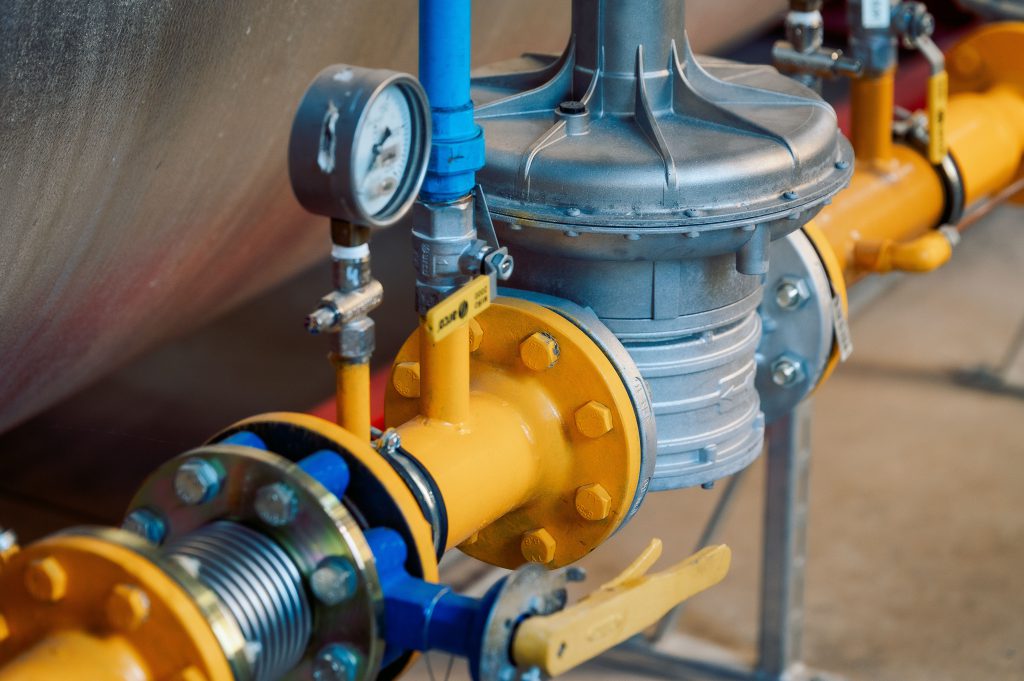
Addressing Downtime with FOCUS-1
To address these challenges, the chemical manufacturer implemented the FOCUS-1 smart meter valve. This solution integrated measurement and control components, simplifying the system and enhancing accuracy. The FOCUS-1’s internal PID controller maintained the desired flow rate and provided feedback on pressure, enabling precise control over the condensate distribution.
Key features and benefits of the FOCUS-1 included:
- Enhanced Control Accuracy: The FOCUS-1 allowed precise control of condensate flow, ensuring efficient distribution to all plants.
- Energy Efficiency: By monitoring before and after pressure, the pump frequency could be adjusted, optimizing energy use.
- Cavitation Detection: The FOCUS-1’s diagnostic capabilities enabled detection and prevention of cavitation, reducing equipment damage and maintenance costs.
- Digital Redundancy: The smart valve’s digital redundancy ensured continuous flow regulation even in case of measurement disturbances, guaranteeing reliable condensate delivery.
Learn more about what a Smart Meter Valve is here:
Impact on Downtime Reduction & Operational Efficiency
The implementation of the FOCUS-1 led to significant improvements:
- Reduced Maintenance Needs: One less trip to the maintenance shop due to the device’s ability to prevent cavitation.
- Energy Savings: Optimized pump energy usage and reduced wear, prolonging pump lifespan.
- Continuous Operation: The ability to compensate for measurement failures ensured uninterrupted processes, reducing the need to activate redundant pumps and preserving their longevity.
Key Learnings from the FOCUS-1 Implementation
From this implementation, it was learned that integrating advanced smart metering solutions like the FOCUS-1 can significantly enhance operational efficiency and reliability. Precise control and monitoring capabilities not only reduce downtime but also contribute to energy savings and lower maintenance costs.
Future Plans for Expanding Smart Meter Valve Use
Encouraged by the success of the FOCUS-1, plans are in place to replace other valves in the system to further enhance efficiency and reduce downtime. This proactive approach aims to ensure more reliable operations and continued energy efficiency improvements.
Conclusion
The experience with the FOCUS-1 smart metering valve demonstrates the significant impact of advanced control solutions in the process industry. By eliminating downtime and optimizing energy use, this leading chemical manufacturer has set a benchmark for efficiency and reliability in condensate distribution systems. This case study serves as a valuable reference for other companies looking to enhance their operations through smart technology and process simplification.