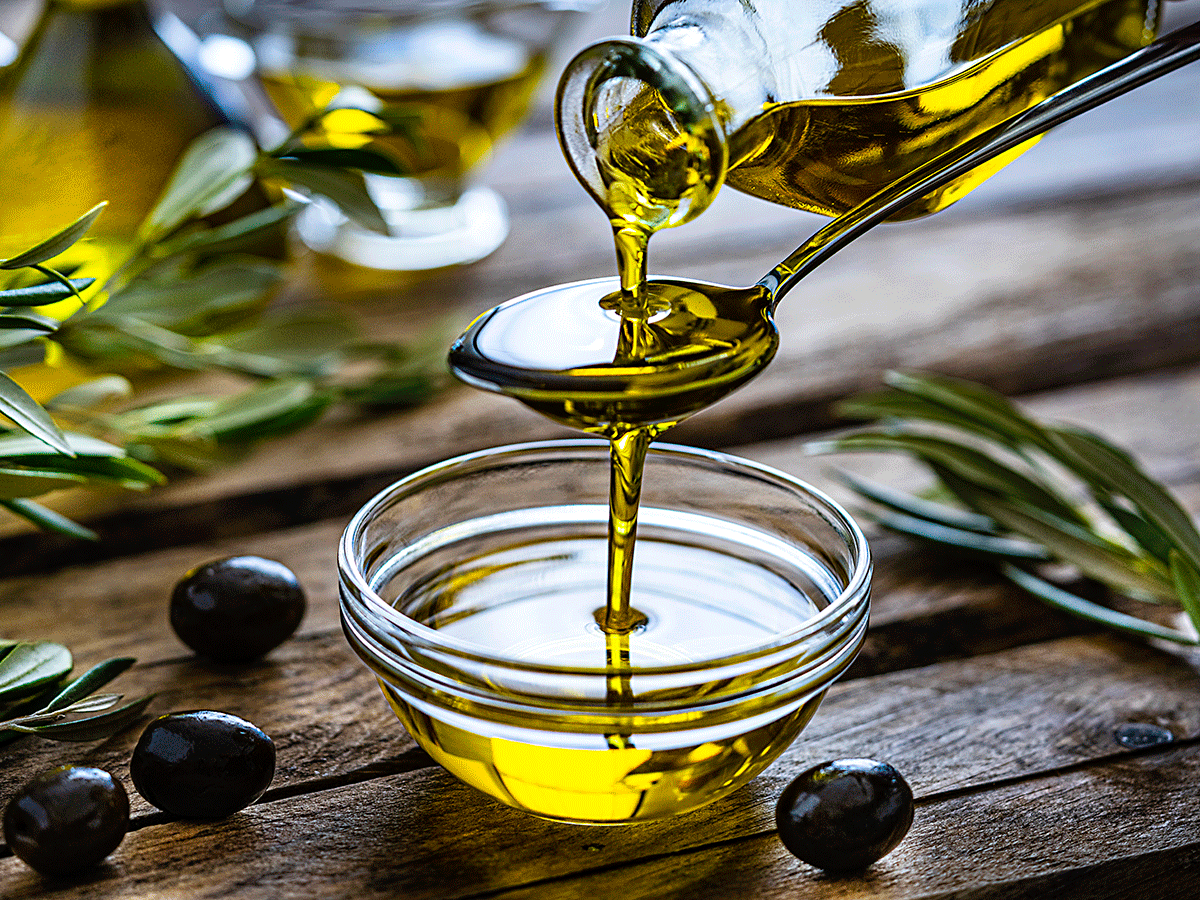
Refining Edible Oil Cooling for Heat Exchangers with FOCUS-1
Discover how Special Refining Company (SRC) transformed its oil cooling process with FOCUS-1, boosting efficiency and control in edible oil refinement.
Discover how Special Refining Company (SRC) transformed its oil cooling process with FOCUS-1, boosting efficiency and control in edible oil refinement.
Explore how ArcelorMittal optimized thermal oil cooling with FOCUS-1. Discover the challenges of traditional setups and see how this smart meter valve technology transformed their steel production process, boosting efficiency, reducing costs, and increasing uptime.
Explore how Dynea, a leader in Europe’s wood adhesives sector, revolutionized boiler efficiency and sustainability with FOCUS-1, the world’s first smart meter valve.
Discover how a German municipal utility achieved precise tank level control, energy efficiency, and reduced maintenance costs using the FOCUS-1 smart meter valve.
Discover how a leading chemical manufacturer in Antwerpen reduced downtime and improved operational efficiency with the FOCUS-1 smart metering valve. Learn about the challenges faced and the successful strategies implemented.
Discover how a global agriculture and food industry leader optimized their gas scrubber operations with FOCUS-1. Learn about improved control, real-time data insights, and increased efficiency in this case study.
In this case study we will explore the traditional waste incineration process, the inherent challenges, and how FOCUS-ON’s innovative smart meter valves have revolutionized operations at the Kristiansand plant. By introducing FOCUS-ON’s smart meter valves, the plant has achieved significant advancements in efficiency and control, overcoming previous limitations.
FOCUS-1 combines flow, temperature, and pressure sensors with controls for optimal alkaline electrolyser performance. Simplifying KOH concentration measurement and flow control, it enhances efficiency, reduces complexity, and lowers costs in hydrogen generation through electrolysis. Precise measurement ensures ideal electrolyser operation during the energy transition to renewable hydrogen sources, aiding the shift from fossil fuels.
An essential aspect of the biorefinery process involves steam production. Their careful regulation of water and steam production is geared towards reducing energy consumption and ensuring a responsible carbon footprint. A crucial element of achieving this lies in the efficient management of condensate return lines, which transport condensate back to the boiler. A important factor for this process is its safety aspects. FOCUS-1 ensures that the boiler feed water tank with the correct amount of water to maintain safe operating conditions.
FOCUS-ON VoF
Kerkeplaat 12
3313 LC Dordrecht
The Netherlands