ArcelorMittal, a global leader in steel production operating across 60 countries, is renowned for its innovation and sustainability efforts throughout the steel manufacturing process. However, maintaining optimal machinery temperatures poses a significant challenge, especially with conventional cooling methods. Focus-ON steps in as a leader in innovative solutions, offering ArcelorMittal enhanced efficiency and reliability. Throughout this case, we will investigate the intricacies of cooling systems, highlight how FOCUS-ON’s FOCUS-1 solution is reshaping the industry, and reveal the concrete benefits ArcelorMittal gains from these advancements. Let’s discover the impact of Focus-ON’s technology and ArcelorMittal’s pursuit of operational excellence in the steel industry.
The Challenge of the Traditional Setup
Ever wondered what keeps steel mills running smoothly? Thermal oil is vital, needing efficient cooling to prevent overheating and ensure continuous operation. Yet, cooling isn’t straightforward—control valves, setpoints, and intricate processes add complexity. Let’s uncover the secrets of thermal oil cooling in steel production and explore steelmaking and innovation together.
The Basics of Thermal Oil and Heat Exchangers
In the world of steel mills, thermal oil is the unsung hero. It’s the go-to for maintaining just the right temperatures in critical machinery like rolling mills and continuous casting machines. But keeping this hero cool is where things get tricky. We use a heat exchanger with water to do the job, but it’s not as efficient as it could be. This setup involves control valves and setpoints that can slow things down and doesn’t give us all the data we need for optimal performance.
Delays and Data Gaps in the Current Operational Setup
Let’s break down our traditional setup. We’ve got control valves, temperature sensors, and a Distributed Control System (DCS) all working together. The temperature sensor communicates with the DCS, which then tells the valve how to act. But there’s a catch – there’s a delay in this communication, which can affect efficiency. Plus, we’re not getting all the measurements we need, making it challenging to fine-tune our operations. It’s a headache, but we’re on the lookout for a better solution.
If you want to know more you can have a look at our blog, “Traditional Process Control Vs. Smart Meter Valves“.
Perfecting Thermal Oil Cooling
Arcelor Mittal’s journey to optimize thermal oil cooling takes a leap forward with FOCUS-1. This innovative solution replaces traditional valves, offering streamlined control and monitoring capabilities. By integrating all necessary components into one device, FOCUS-1 provides valuable insights into heat exchanger efficiency. How does this technology transform Arcelor Mittal’s operations? What are the key benefits of integrating FOCUS-1 for thermal oil cooling?
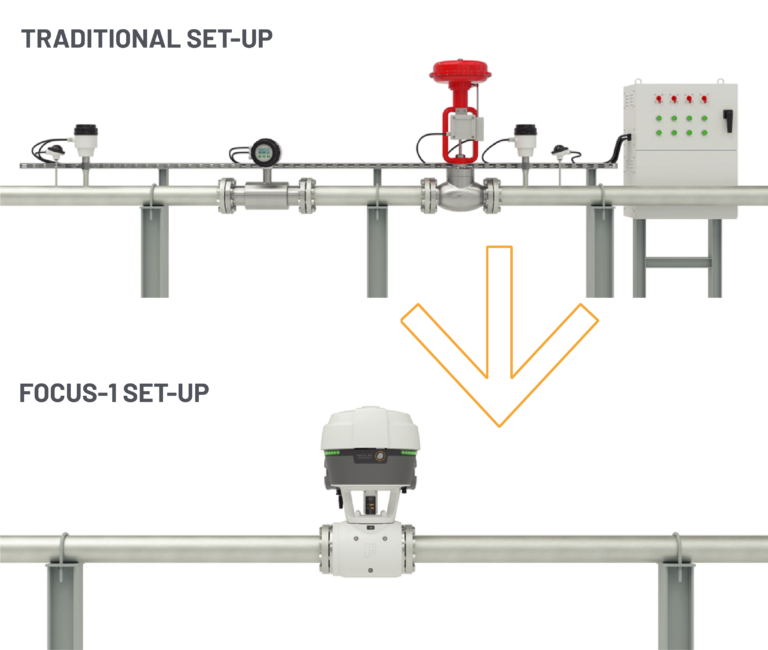
Improved Control and Monitoring
In the dynamic environment of the steel mill, precision is crucial. FOCUS-1 revolutionizes control and monitoring, offering a comprehensive solution in a single device. By replacing traditional valves with FOCUS-1, operators enjoy seamless integration of all control and monitoring functions.
Gone are the days of managing multiple sensors and systems. With FOCUS-1, temperature sensing and flow control are effortlessly combined, guided by an internal PID controller for optimal valve positioning and flow rates.
This streamlined approach eliminates complexities, ensuring precise control and efficient operations.
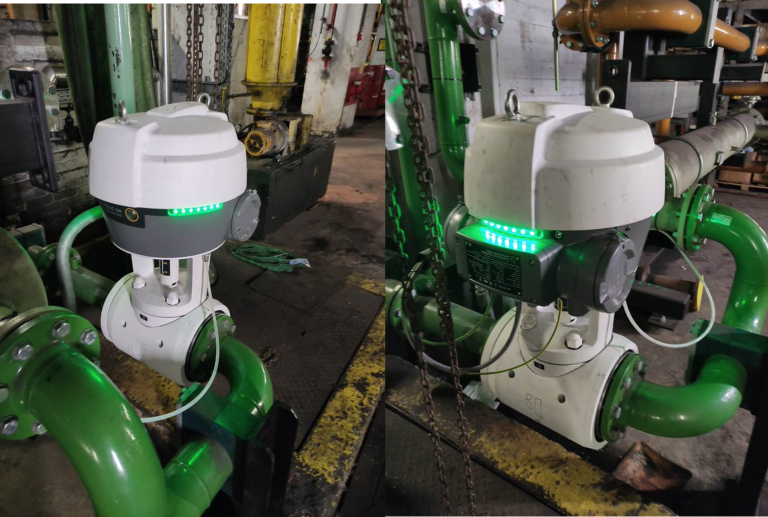
How FOCUS-1 Upgraded ArcelorMittal’s operations
Finally, we will look into the benefits that Focus-1 offers to the steel industry. How do Focus-ON’s smart valve meters enhance thermal oil cooling? How can we address the industry’s complexities to achieve greater efficiency and sustainability?
- Space and Cost Savings: Integration of FOCUS-1 consolidates multiple functions into a single device, reducing installation complexity and costs.
- Enhanced Cost Efficiency: FOCUS-1 combines flow measurement, analytic measurement, and control capabilities, resulting in cost savings.
- Fast and Accurate Measurement: FOCUS-1 provides swift and precise KOH concentration measurement, facilitating efficient control.
- Optimal Control Performance: Utilization of high measurement frequency and digital twin technology ensures reliable operation.
- Comprehensive Control and Monitoring: FOCUS-1 offers valuable insights with comprehensive control and monitoring capabilities.
- Improved Operational Efficiency: Enables accurate, stable, and fast flow control, enhancing efficiency.
- Increased Uptime: Provides additional data insights for higher uptime and continuous operation, optimizing performance in steel production.
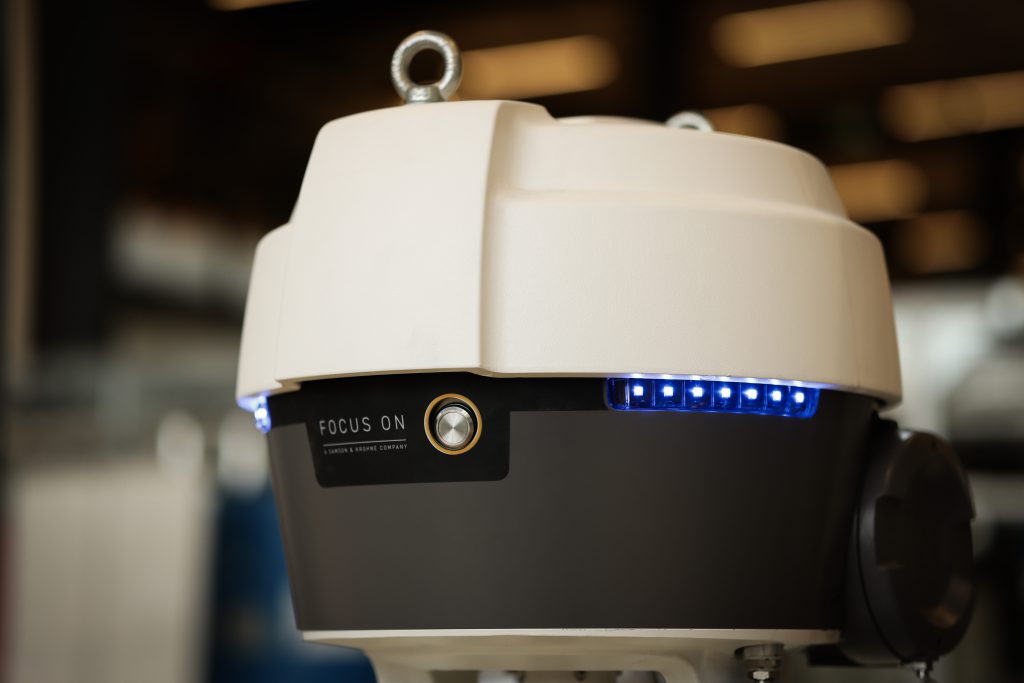
Curious About the FOCUS-1 Benefits for You?
Get in touch to talk about the benefits of the FOCUS-1, to plan a demo or to talk about the possibilities of a proof-of-concept!