How in Steel Production Smart Meter Valves Reduce Downtime
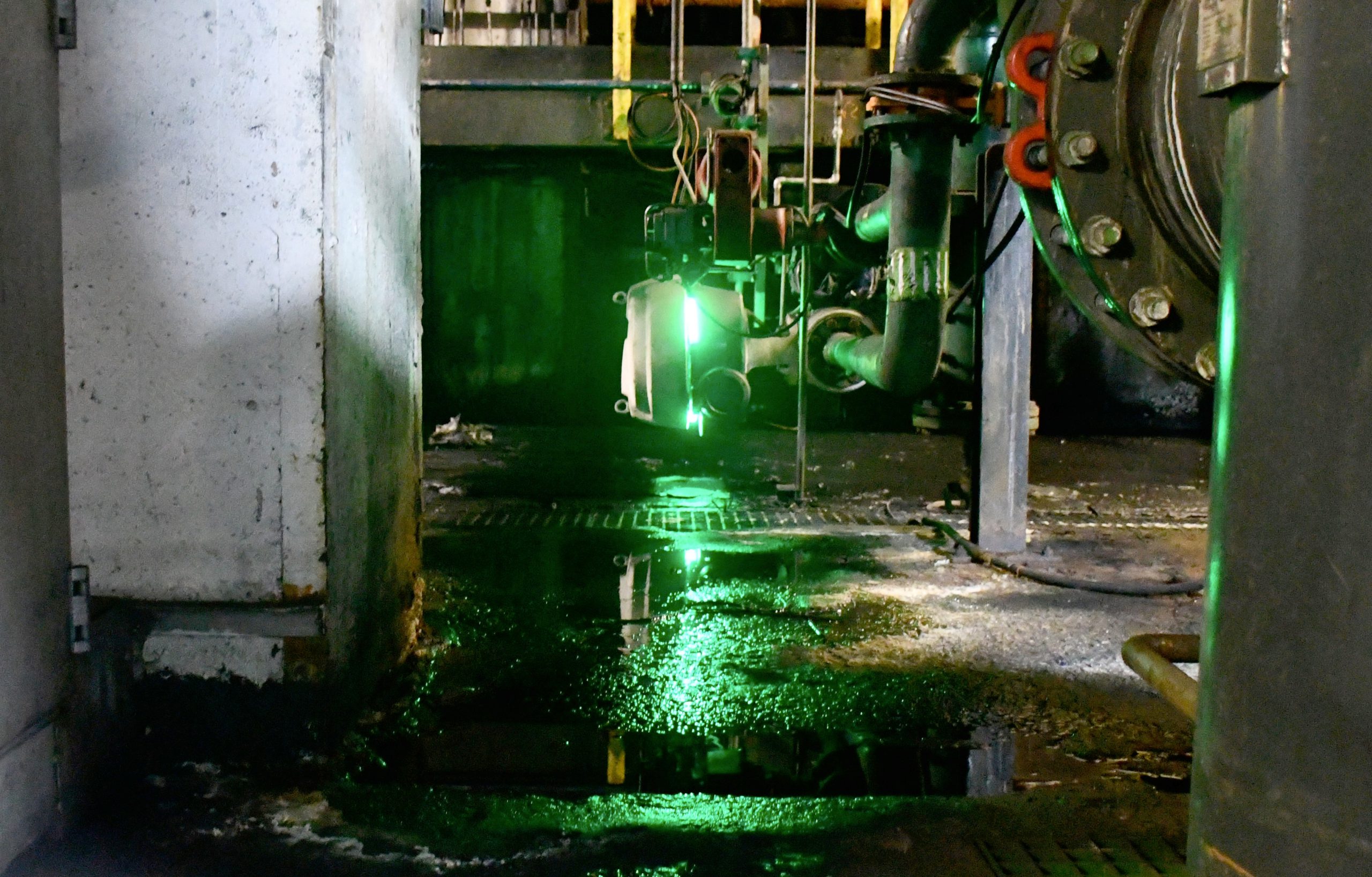
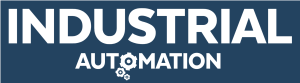
Published by Industrial Automation
Platform & Magazine
January, 2025
No conditions expose measurement and control instruments more than a steel production process.
At the hot rolling mill of ArcelorMittal Belgium in Ghent, FOCUS-1 smart control valves prove their value. They ensure that the precise amount of water is sprayed between the steel plate and the mill: a critical step in producing high-quality steel coils.
Besides better control, these valves provide extensive diagnostic capabilities that have already helped prevent multiple production shutdowns.
The Control Challenge in Steel Production
Rolling Process Overview
Steel slabs up to 22 cm thick are processed in the roughing mill of ArcelorMittal, where they are reduced to 3 cm. Then, they are passed through the finishing mill and transformed into plates between 1.25 mm and 13 mm thick. These are either shipped as coils or sent to cold rolling for further processing.
Automation Zones and Skin Cooling Demands
The hot rolling mill at ArcelorMittal Belgium is divided into two automation zones: “furnaces-roughing” and “finishing mill/coilers.”
“During finishing, pick-up is a particularly time-critical process for surface quality,” explains Filip Vanhaelst, coordinator of automation technicians for the finishing-mill. “Skin cooling, in this case water, must reach the exact spot between the plate and the mill at the right moment. If it’s too late, the mill burns. Too early, and the plate won’t be properly gripped for rolling.”
Why Traditional Instrumentation Falls Short
Legacy Setup Limitations
Previously, the system used a separate valve and flow meter. According to control technician Niels Van De Walle:
“This setup lacked diagnostics. We could extract some data from the flow meter, but had no insight into valve position or status. That meant we often detected problems too late, resulting in lost product and valuable production time.”
The Need for Integrated Control
With separate components, operators lack real-time process visibility. The complexity increases installation and maintenance efforts while limiting opportunities for predictive action.

From left to right: Filip Vanhaelst (ArcelorMittal Belgium), Niels Van De Walle (ArcelorMittal Belgium), Wim Lintermans (KROHNE) and George Borst (FOCUS-ON).
Discovering FOCUS-1: The Smart Control Valve for Steel Industry
A Joint Innovation by KROHNE and SAMSON
During a trade fair, the team of ArcelorMittal discovered FOCUS-1. A smart control valve that integrates:
- Flow measurement
- Pressure and temperature sensing
- Valve actuation and control
- Built-in diagnostics
“Together, we can build and maintain control loops with a single product,” explains George Borst, business development and marketing manager at FOCUS-ON.
Diagnostic Power and Space Efficiency
FOCUS-1 offers pre-programmed diagnostic models for:
- Cavitation and flashing
- Valve wear, air leakages and more
- Flow and pressure trend analysis
With all features embedded in one compact device, FOCUS-1 eliminates the need for multiple instruments and saves 33% on installation costs.
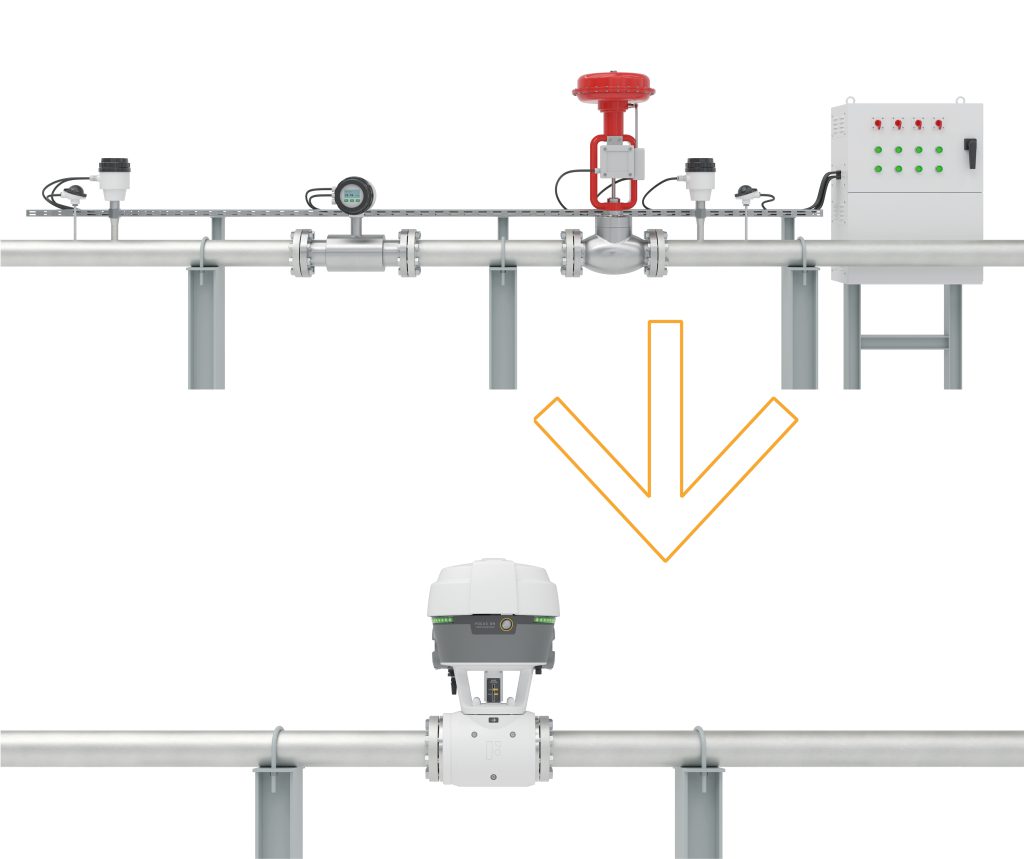
FOCUS-1 can replace a traditional control loop with 1 device, saving space, reducing complexity and installation costs with 33%.
Field Test at Steel Plant ArcelorMittal: Proving Performance
Pilot Setup in the Hot Rolling Mill in Steel Production
To validate its capabilities, ArcelorMittal installed FOCUS-1 next to their existing valve under real operating conditions.
“We demand faster control response times than most industries,” explains Vanhaelst. “Initial tests didn’t meet our < 0.7-second goal. But with software updates and a larger compressed air supply, we now exceed that benchmark.”

Control graph of FOCUS-1 with reference flowmeter. Top graph, blue: flow setpoint, red: reference flowmeter and green: FOCUS-1 flow. Bottom graph, blue: valve setpoint, red: valve position feedback.
Gaining Process Visibility
Thanks to pressure sensors at both the valve’s inlet and outlet, engineers could:
- Monitor cooling water flow in real-time
- Identify closed shut-off valves
- Trigger alarms for non-functioning components in the same line
The Power of Diagnostics
Detecting Failures Before They Escalate
“We’ve made real progress. In the last six months of using the old valves and controllers, we frequently had failures. With FOCUS-1, we identify issues instantly,” says Van De Walle.
Example: During a startup, a compressed air supply issue was immediately detected, minimizing downtime during the critical start up phase.
Built-In Redundancy for Peace of Mind
“FOCUS-1 features built-in redundancy. It uses a digital twin to simulate expected behavior. If the flow sensor fails, it can estimate flow based on differential pressure,” says Vanhaelst.
Preparing for the Future: Scalability and Integration
Integration into Existing Systems
FOCUS-1 was integrated into ArcelorMittal’s DCS via PROFINET, enabling full data visualization and alarm integration.
Looking Ahead for Steel Plant ArcelorMittal
“Whenever we need a new valve or need to retrofit an existing one, this will be high on our list, especially once it’s available in larger diameters,” Vanhaelst concludes.
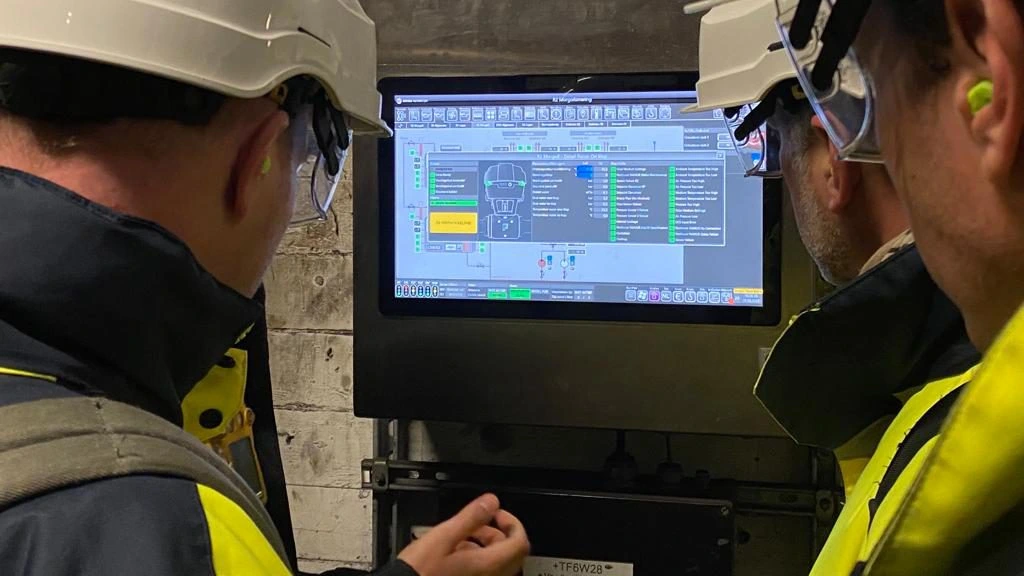
Integration into DCS of Arcelor Mittal with PROFINET. Visualization of all the data and alarms that can be retrieved of FOCUS-1.
Before vs. After: Measurable Gains of ArcelorMittal with FOCUS-1
1. Fast control setup
- Before: Legacy system was optimized to meet critical reaction time with separate sensors and valve.
- With FOCUS-1: Optimized system achieved < 0.7 seconds response time and more stabilized flow data.
2. Downtime Reduction
- Before: Frequent issues with valves and controllers, leading to production delays.
- With FOCUS1-: Immediate issue detection (e.g., compressed air failure at startup), preventing multiple unplanned shutdowns.
3. Defect Detection Time
- Before: Valve status, pressure and flow not linked and faults detected too late.
- With FOCUS-1: Real-time diagnostics catch issues instantly, for example using pressure information to catch blocked pipes or closed valves.
4. Digital Redundancy
- Before: No redundancy, when a flowmeter fails this resulted in a cooling failure.
- With FOCUS-1: Simulates expected process behavior and enables redundant flow measurement via differential pressure if sensor fails.
5. Valve & Sensor Footprint
- Before: 1 control valve, 1 pressure sensor + 1 flow meter
- With FOCUS-1: 1 compact device, reducing:
- Installation complexity
- Maintenance needs
- Space requirements
- Saves 33% on installation of the control loop
Conclusion: Why Smart Valves Belong in Steel Plants
For ArcelorMittal Belgium, FOCUS-1 smart control valves deliver more than improved flow regulation. They offer real-time insights, built-in resilience, and simplified architecture.
This case shows what’s possible when smart field-level technology is used to its full potential. The result? Fewer shutdowns, faster startups, and higher process quality.
Read more case studies here.
Book your free consultation call today!
Want to read more about FOCUS-1?
Also make sure to read our blogs about: