Established in 1996, Special Refining Company (SRC) refines vegetable oils and fats as a service-oriented subsidiary of the Pieter Bon Group. The complex process of oil refinement demands precise control and monitoring, with conventional methods proving inefficient. Enter FOCUS-ON, a pioneer in innovative solutions for the food industry. In this case, we’ll explore how Focus-ON’s FOCUS-1 solution revolutionized SRC’s operations. First, we’ll analyze traditional cooling setups, then the optimization achieved through Focus-ON, and finally, the transformative benefits for SRC’s operations. This partnership exemplifies how cutting-edge technology can enhance efficiency and drive innovation in edible oil refinement.
Decoding Traditional Setup Challenges
Let’s start by examining the complexities of traditional heat exchanger setups and their role in edible oil cooling. What makes these systems crucial for SRC? How does the conventional approach impact efficiency and oil quality? By understanding these fundamentals, we’ll identify the challenges faced by SRC and set the stage for the transformative solutions to come.
What You Need to Know About Heat Exchangers and Edible Oil Cooling
Heat exchangers are vital for SRC, cooling raw or refined oil to the right temperature for further refining or storage. This cooling process is crucial for maintaining oil quality and minimizing potential damage. Efficient heat exchanger operation also aids in reducing SRC’s carbon footprint by capturing residual heat from the refined oil to warm water, optimizing energy reuse in production.
The Typical Heat Exchanger Applications
Traditionally, in conventional heat exchanger applications, a control valve is installed, and a setpoint is provided to regulate the valve opening percentage. The valve’s opening is determined by the process fluid temperature on the cooling water outlet side of the heat exchanger. A temperature sensor measures this temperature and communicates with the Distributed Control System (DCS), which then generates the setpoint for the valve.
However, this setup introduces latency that can affect the efficiency of the heat exchanger. Additionally, a traditional setup lacks comprehensive measurements, which limits the ability to perform detailed analysis of the heat exchanger’s efficiency. The lack of real-time data and the delay in communication between sensors and the DCS make it challenging to fine-tune operations, leading to inefficiencies and potential quality issues.
Understanding these challenges highlights the need for innovative solutions that enhance control and monitoring capabilities, paving the way for SRC’s operational excellence.
Transforming Edible Oil Cooling
Moving on, we will research how the integration of FOCUS-1 revolutionizes edible oil cooling operations at SRC. How does this technology enhance control and monitoring? What benefits does it bring to the efficiency of heat exchangers? By analyzing these questions, we will understand the significant improvements achieved through this innovative solution.
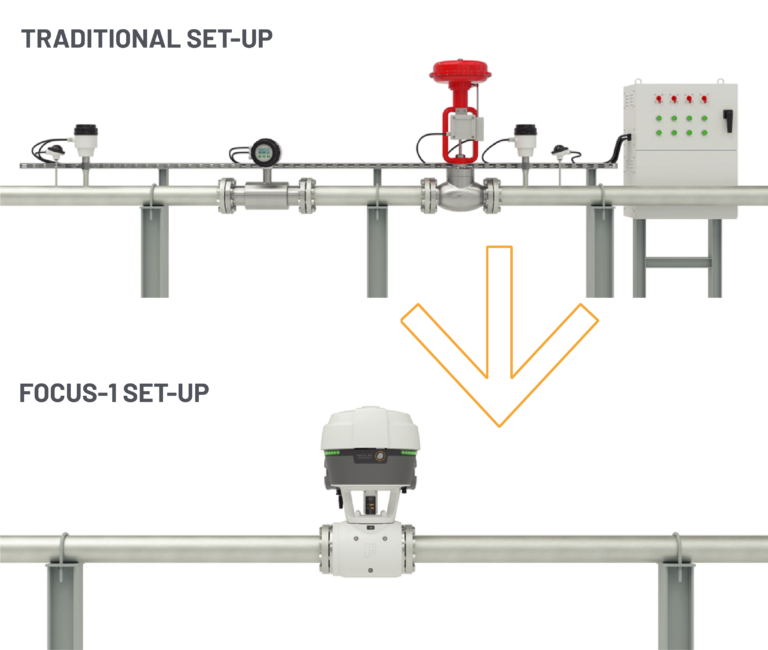
Optimized Control and Monitoring
By replacing the traditional valve with FOCUS-1, SRC gains advanced control and monitoring capabilities along with valuable insights into the heat exchanger’s efficiency. FOCUS-1 combines all necessary measurement and control components into a single device, enabling operators to make informed decisions based on real-time data, regardless of changes in process conditions.
Instead of relying on a separate temperature sensor connected to the DCS to determine the control valve setpoint, the temperature setpoint can be directly provided to FOCUS-1 via conventional communication protocols. The internal PID controller within FOCUS-1 then determines the optimal valve position for the desired flow rate, ensuring precise and efficient control.
This integration not only simplifies the control setup but also enhances the overall efficiency and reliability of the edible oil cooling process. By eliminating the latency and limited data collection of traditional setups, FOCUS-1 enables SRC to achieve superior performance and maintain high-quality standards in its operations.
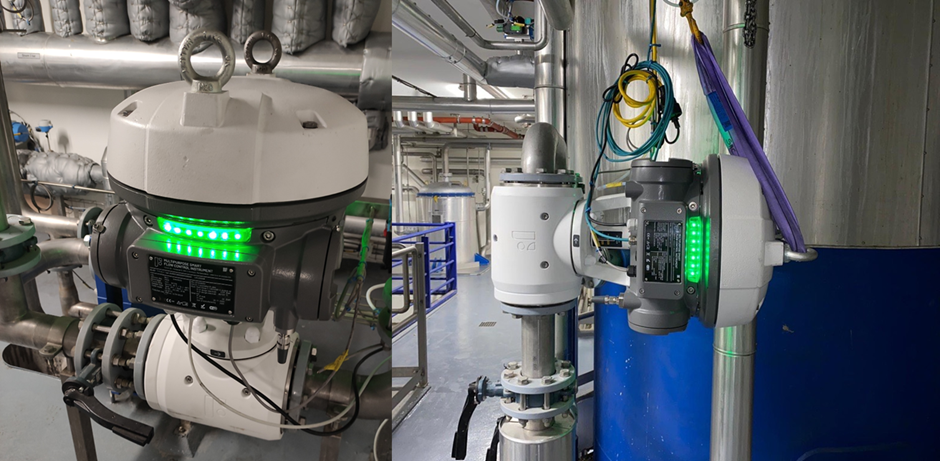
How Smart Meter Valves Enhanced SRC’s Operations
In outlining the advantages of adopting smart meter valves over conventional setups, the benefits emerge as profound. Specifically tailored to address the needs of leading industry players, such as SRC, the advantages of integrating FOCUS-1 into their operations are multifaceted and impactful.
- Enhanced control and stability for improved heat exchanger performance
- Reduced energy consumption during variable production demands
- Comprehensive data collection and analysis by FOCUS-1
- Prompt detection and response to process changes
- Extended equipment lifespan and minimized operational expenditure
- Integration of control valves, flowmeters, pressure, and temperature sensors into a single device
- Reliability and longevity ensured by standard SAMSON & KROHNE components with redundant design
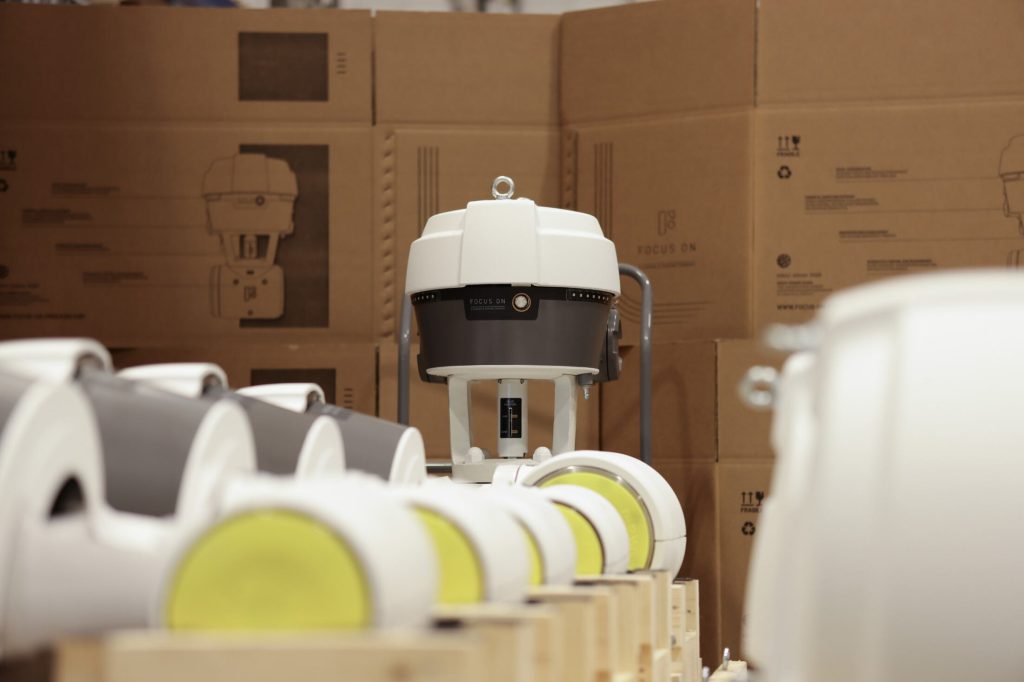
Curious About the FOCUS-1 Benefits for You?
Get in touch to talk about the benefits of the FOCUS-1, to plan a demo or to talk about the possibilities of a proof-of-concept!