In the water supply industry, ensuring precise and reliable level control of drinking water tanks is crucial to maintaining continuous service and preventing costly disruptions. This case study showcases how a municipal utility in eastern Germany optimized their water supply system by implementing the FOCUS-1 smart metering valve, achieving enhanced control, energy efficiency, and operational reliability.
Overview of the Water Utility
A municipal utility in eastern Germany manages two essential water towers to ensure a continuous supply of drinking water to nearby communities. The water, sourced from various treatment plants, meets high-quality standards despite a high lime content. To overcome this challenge, the utility plans to switch to a remote reservoir connected via a long-distance pipeline. Accurate and reliable process control is crucial for this setup.
Traditional Setup Limitations
To address the high lime content in the current water supply, the municipal utility decided to switch to a remote reservoir using a long-distance pipeline. The new pipeline (DN300) operates at a pressure of 10–13 bar (145–188.5 psi). Precise control of the tank level and inlet pressure is necessary to prevent damage from excessive differential pressures and cavitation. Traditional methods using piston-actuated control valves, flow and level instrumentation, and process automation were complex and costly.
Control Requirements and Challenges
Implementing the new pipeline system came with several challenges that needed to be addressed to ensure reliable and efficient operation.
High Lime Content and New Pipeline Requirements
The transition to a remote reservoir required accurate control to maintain the desired tank level and prevent infrastructure damage due to high differential pressures and cavitation.
Precise Control Requirements
The long-distance pipeline (DN300) operates at pressures between 10 and 13 bar (145-188.5 psi). The utility must regulate the supply to the elevated tanks, maintaining precise pressure control to prevent infrastructure damage due to excessive differential pressures and cavitation.
Risk of Cavitation
Cavitation, the implosion of gas bubbles, can cause significant damage due to localized pressure spikes. The utility previously relied on a combination of piston-actuated control valves, flow and level instrumentation, and process automation to mitigate this risk.
Energy and Cost Concerns
Maintaining emergency power capacity for conventional electric control valves, which require 3-4 kW, is a significant cost factor. The utility sought a simpler, more cost-effective solution, favoring pneumatic control valves with a maximum power consumption of around 15 W.
Downtime Risks
Failure of traditional control valves and components could lead to significant downtime and costly repairs. Maintaining emergency power capacity was also a major cost factor.
Taking these challenges into account, FOCUS-1 was implemented.
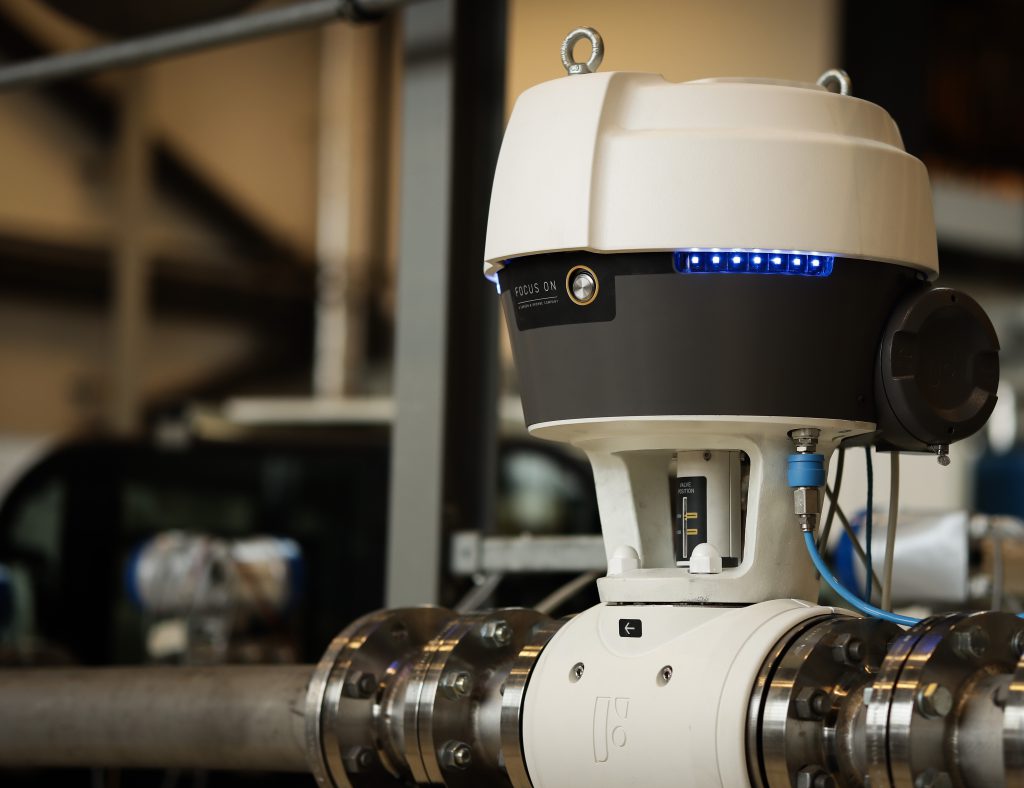
Implementing the FOCUS-1 Solution
The utility opted for the FOCUS-1 smart metering valve, which combines sensors, actuators, and a control valve. This integrated device allows for setpoints control of pressure, flow rate, or external control variables.
Pneumatic Operation
Unlike electric valve actuators, the FOCUS-1 operates pneumatically, requiring only a constant supply of compressed air. Its integrated compressed air preparation ensures maintenance-free and leak-free operation, enhancing energy efficiency.
Cavitation Prevention
FOCUS-1’s sophisticated algorithms and design ensure that the control valve and outlet remain outside the cavitation area. This prevents damage and extends the lifespan of infrastructure components.
Digital Twin and Redundancy
The intelligent measuring valve creates a digital twin, maintaining device function even if a sensor fails. This digital redundancy ensures continuous operation and data transmission via PROFINET for condition-based maintenance.
Customer Benefits and Results
Enhanced Control and Efficiency
- Precise Level Control: FOCUS-1 reliably maintains the desired tank level setpoint.
- Energy Savings: Pneumatic operation reduces power consumption significantly compared to traditional electric valves.
- Cavitation Diagnostics: Prevents damage caused by spontaneous pressure loads.
Simplified Maintenance
- Maintenance-Free Operation: Integrated compressed air preparation ensures long-term, maintenance-free performance.
- Condition-Based Maintenance: Real-time data transmission and diagnostics enable proactive maintenance.
Conclusion
This case study highlights the transformative impact of integrating advanced smart metering solutions like FOCUS-1 in water supply systems. By enhancing control accuracy, preventing cavitation, and optimizing energy use, the utility achieved significant operational improvements and cost savings. For more insights on process optimization, explore our related blogs on process simplification and smart meter valves.